How we make our products is just as important as what we make, so we consider our impact at every step.
More than 165 years ago, we created the blue jean as a response to the people’s need for pants durable enough to withstand the toll of prospecting in the California hills. Today, we manufacture our products with the same responsive spirit. As a company with a global supply chain, however, it’s not just consumers we need to respond to, but also the people who make the garments, the communities in which they are assembled, and the resources of this planet that we all share.
Every step matters – our Terms of Engagement, the water we use (and increasingly recycle and reuse), the chemicals we keep in and out of our supply chain, the people who assemble our products and the processes that determine our carbon footprint. Shaped by data and driven by innovation, we are adapting at every step of the manufacturing process to make it more sustainable, and sharing what we learn with others to catalyze systemic change across the apparel industry.
This is how we respond to what’s needed today – and build the strongest company for the long term.
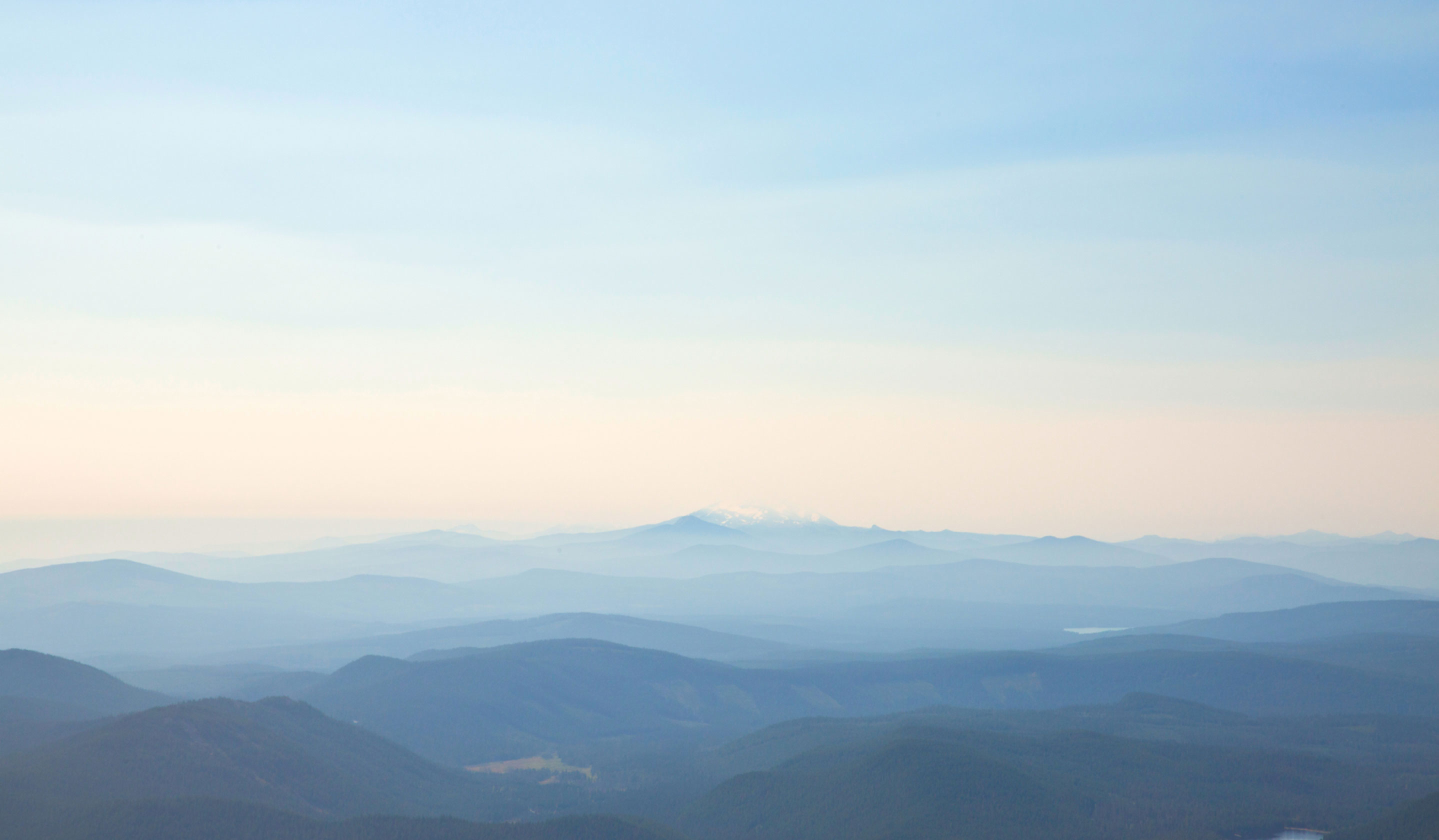

Water
Making jeans is a very thirsty process; present methods use more water in a year than the U.S. has drinking water. This is too much.
Our Plan
Reduce our water footprint across the board with a special focus on water-stressed areas.
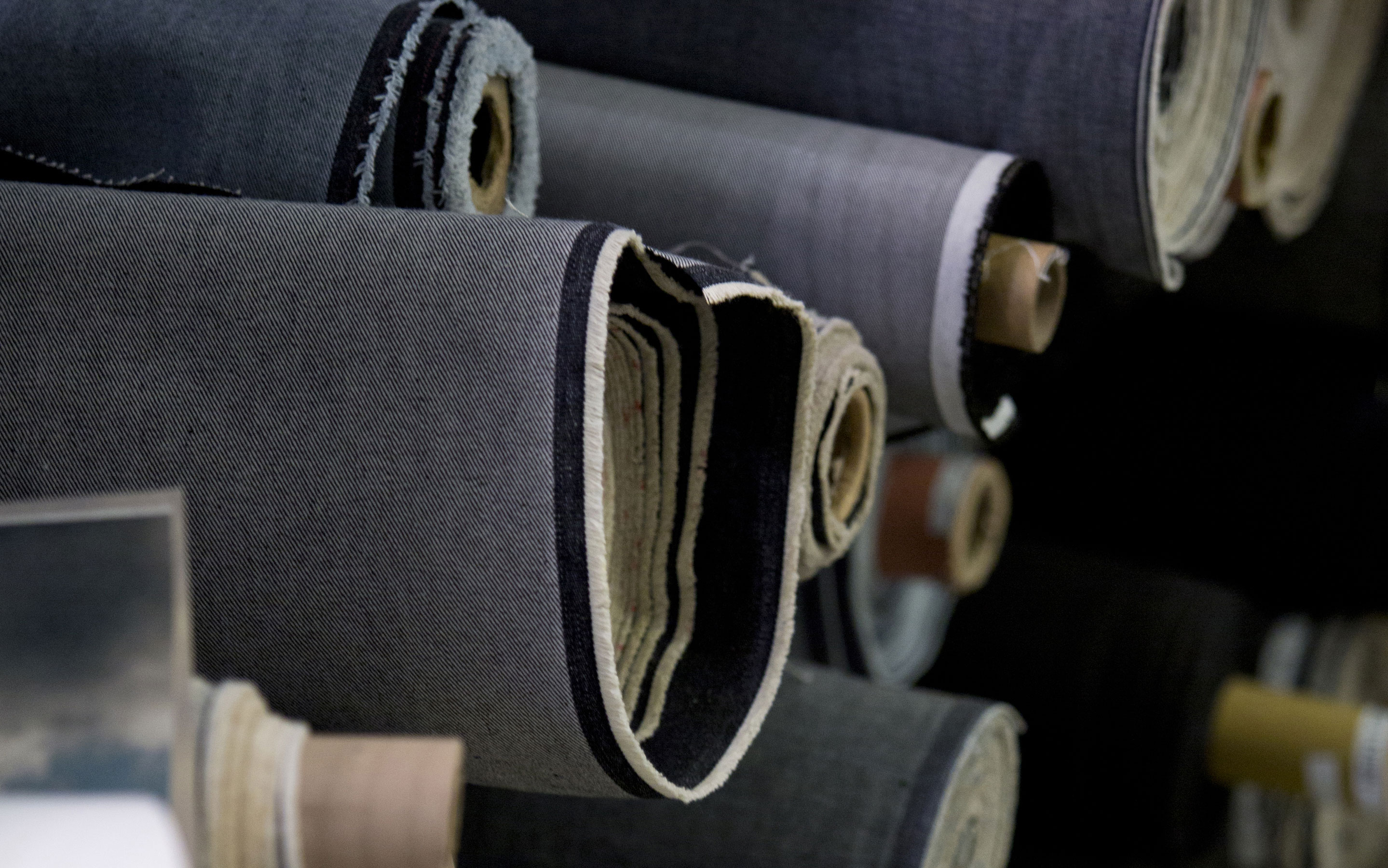
Climate
Thirty-one percent of carbon emissions in our supply chain comes from fabric production, 9% from the garment assembly process, and 6% from processes such as the manufacturing of items like buttons, zippers, rivets, snaps and stitching.
Our Plan
Reduce greenhouse gas emissions by 90% in our owned-and-operated facilities and 40% in our entire supply chain by 2025.
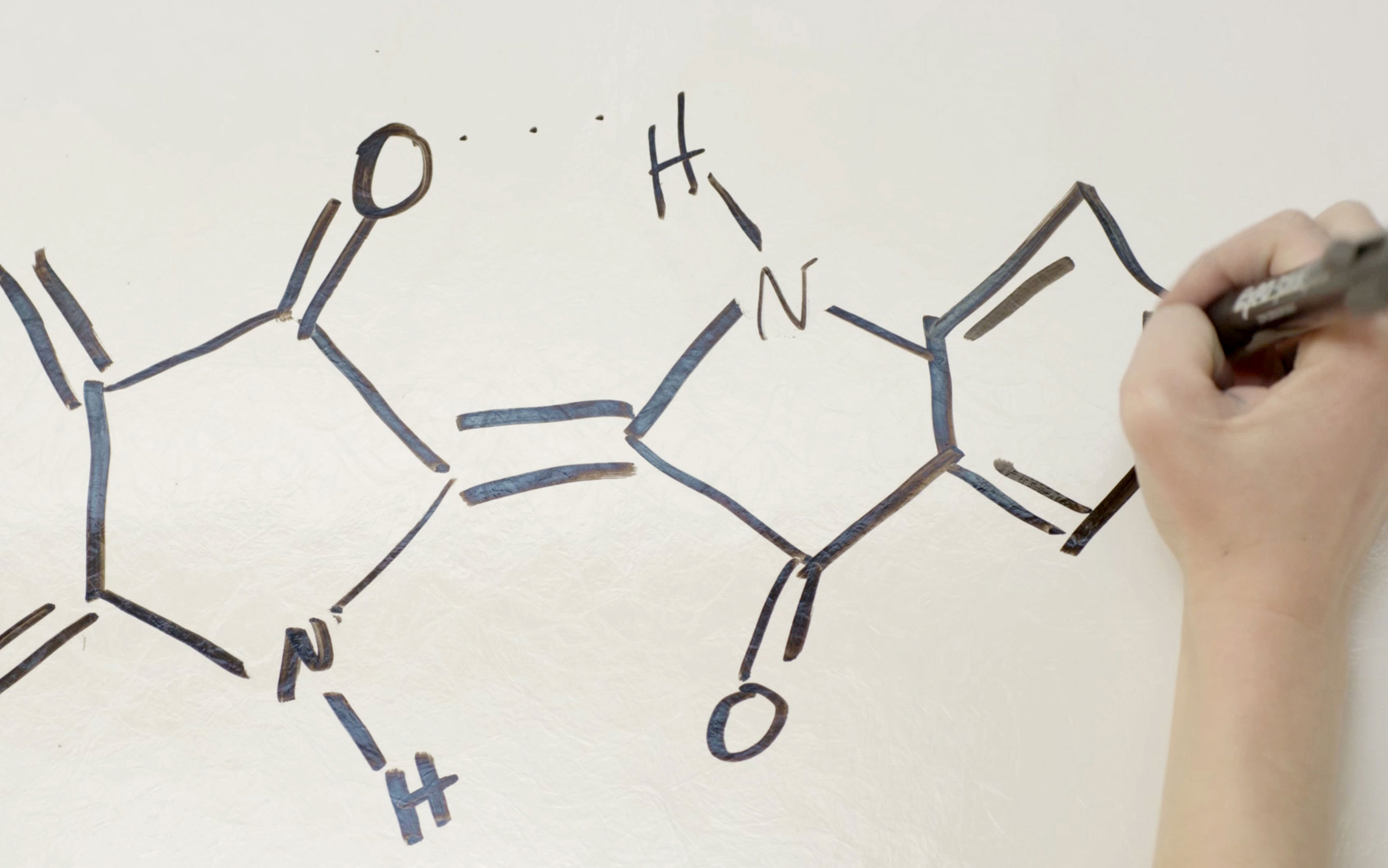
Chemicals
It takes about 3 1/2 times more chemicals than cotton by weight to make, dye, and care for a pair of jeans.
Our Way Forward
Having reached 100 percent Zero Discharge goal in early 2020, continue to share Screened Chemistry and form new partnerships to deliver safer chemistry.
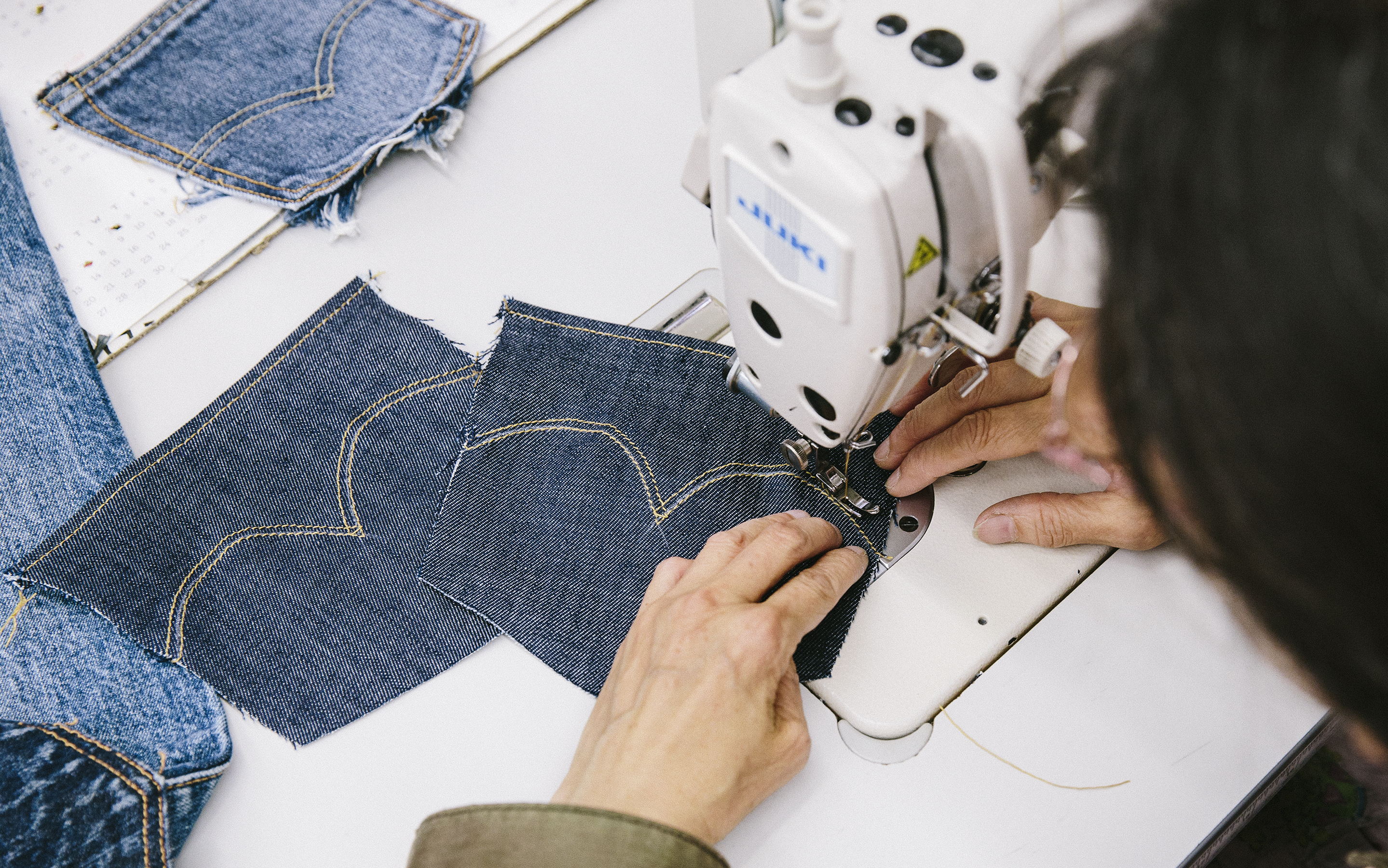
People
We must consider how we can positively impact the women and men who work throughout our supply chain.
Our Plan
Having met our 2020 goal of reaching 200K workers through Worker Well-being a year early, we are now shaping the next iteration of the program.
LS&Co. has a long history of leadership in water use in our industry. In 1994, we were the first apparel company to establish strict water quality standards for suppliers. In 2011, we began implementing the Water<Less® process in our design and manufacturing pipeline. And in 2019, we introduced our 2025 Water Action Strategy, which set contextual water use targets for suppliers and mills that will help us to reduce water use in manufacturing by 50 percent in water-stressed areas by 2025; enhanced the definition of Water<Less® to signify products that come from facilities that meet those targets; and called for collective action to fortify surrounding watersheds in places we operate. Shop Water<Less®.
Screened ChemistryIn 2013, we released Screened Chemistry to help understand the potential health and environmental impacts of chemicals before they enter the supply chain, and to find alternatives for anything deemed unsafe. Three years later, we open-sourced the program, and in 2019, we converged the Screened Chemistry protocol with other apparel brands, including Nike, H&M and C&A, to define a single standard for chemical screening that is now overseen by the ZDHC Foundation, creating a holistic approach to tackling issues of hazardous chemicals and driving innovation in the apparel industry. At the end of 2019, 120 of our key garment and fabric suppliers and 200 chemical suppliers were implementing Screened Chemistry in their facilities. Learn more.
Project F.L.X.Since it was first introduced in 2017, we have continued to refine and expand the use of our Project F.L.X. laser-based finishing technology, which simplifies chemical management by helping to reduce the number of chemicals required in the finishing process from more than a thousand to around a dozen, and which now powers our customizable Future Finish online consumer option. Learn more.
Worker Well-beingLaunched in 2011, LS&Co.’s Worker Well-being (WWB) initiative aims to improve the lives of the women and men who make our products with factory-based programs that address issues related to health, financial security and gender equality. We set a goal to reach 200,000 workers in our supply chain through our WWB programs by 2020. We surpassed that goal in May 2019, and by year’s end, we had reached 219,000 workers in 113 factories in 17 countries, representing more than 65% of total product volume. Learn more here.
Gender Equity in the WorkplaceIn recent years, we have expanded our work to combat gender inequality in the supply chain, building on the Gender Equity Report published by the Levi Strauss Foundation in 2018. We work with industry experts to pursue impactful systemic changes that address the power imbalances between largely female workers and predominantly male managers. To improve the assessment process, we require that all assessment teams include female members and, where possible, female leaders, and we continue to collaborate with partners such as Better Work in Cambodia, Swasti in India, and GEAR in Bangladesh to advance the effort.
Expanding PaCT to new marketsA key facet of our work to meet our science-based targets on climate is our ongoing partnership with the International Finance Corporation (IFC) and its Partnership for Cleaner Textiles (PaCT), through which the IFC provides low-cost financing to suppliers seeking to improve their water and energy use performance. Starting in 2017, we piloted this work with six suppliers in four countries. In 2019, seeing both the sustainability and the financial gains achieved in participating factories, we started to expand our work with IFC/PaCT to 46 of our biggest suppliers and mills across 10 countries.
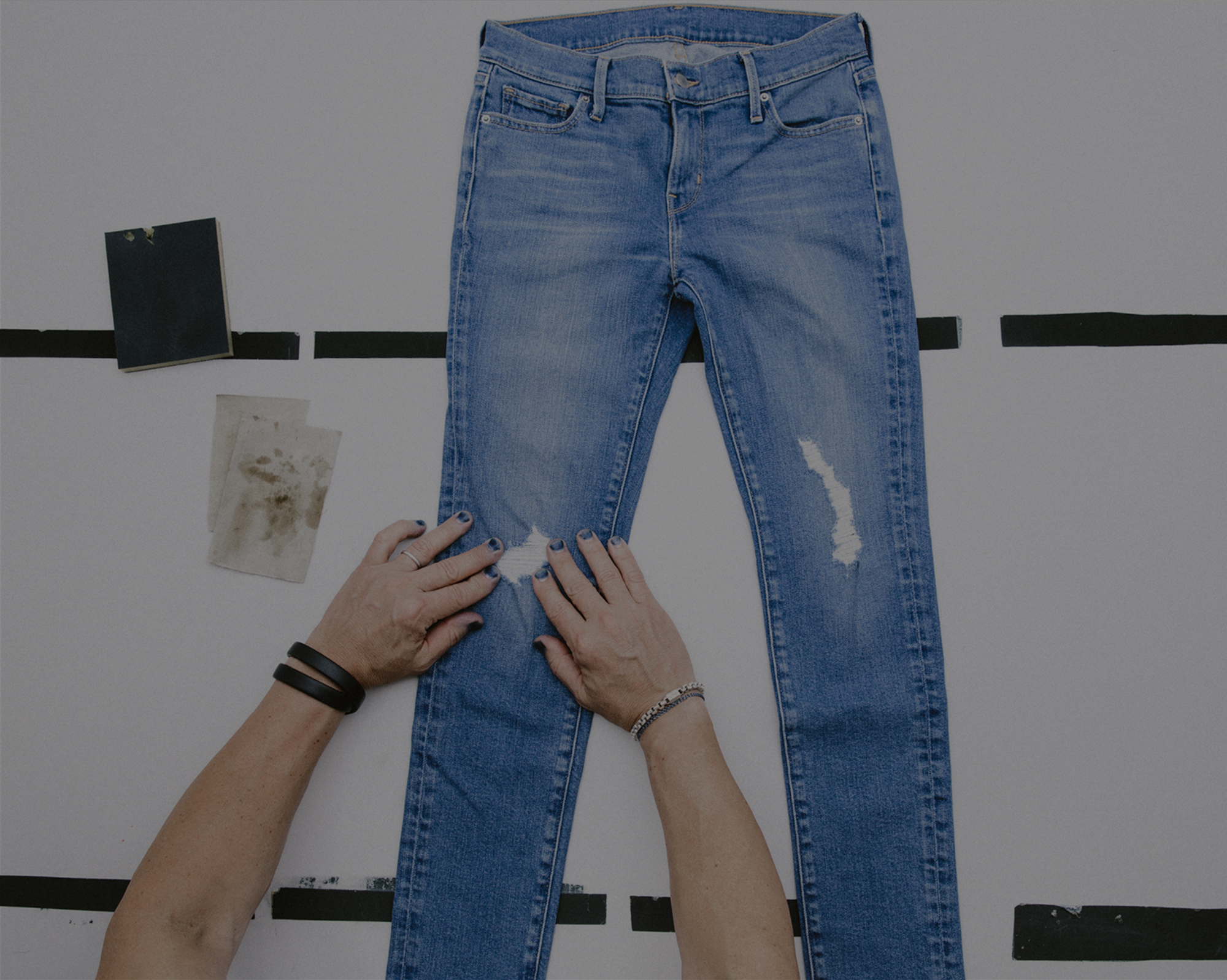